Distretto Circolare Verde
Fonte: Il Gazzettino di Gela del 4 maggio 2022
Inceneritore? No, è una bioraffineria 2.0 – il Gazzettino di Gela
Primo confronto ufficiale, questa mattina a Palazzo di Città, tra l’amministrazione comunale guidata dal Sindaco Lucio Greco e la Maire Tecnimont, la società che, nel caso in cui dovesse essere realizzato a Gela, si occuperà della realizzazione e della gestione dell’impianto che riceverà e smaltirà fino a 400mila tonnellate annue di rifiuti.
Insieme alla sua squadra, all’incontro era presente l’avv. Tommaso Cassata in rappresentanza di Asja in Ati, che è partner del progetto, l’ing. Giacomo Rispoli è amministratore delegato di Myrechemical, società controllata dal gruppo Maire Tecnimont; l’ing. Giacomo Rispoli, amministratore delegato della Maire Tecnimont, che ha illustrato tecnicamente e nel dettaglio al Sindaco, agli assessori Terenziano Di Stefano, Ivan Liardi, Danilo Giordano e Cristian Malluzzo, e all’ing. Pietro Inferrera, il progetto di “Distretto Circolare Verde”, o bio raffineria. La società ha chiesto espressamente che non si parli più di termovalorizzatore o inceneritore, trattandosi di un sistema tecnologico di ultima generazione che non emette sostanze nocive o ceneri tossiche e non produce scarti da trasferire in discarica.“Ci sono 511 discariche in Sicilia, – hanno detto i relatori – molte delle quali sono esaurite, e noi vogliamo contribuire a svuotarle. Nel caso in cui il progetto dovesse concretizzarsi, ci vorrà un anno per il progetto definitivo, che prevede anche la realizzazione di opere civili e montaggi meccanici, e ne serviranno altri tre per l’avvio. Poi occorreranno poi circa 200 dipendenti per far funzionare il tutto, partendo dall’acquisizione del know how di Eni e dall’assunzione di giovani diplomati e laureati per i quali, nella prima fase di preparazione, è previsto un periodo di affiancamento tecnico. Fondamentali inoltre, saranno lo scambio e la collaborazione con l’università del territorio”.
Il progetto integra diverse tecnologie per la transizione energetica e le mette al servizio di un processo di economia circolare da un lato, e di decarbonizzazione dall’altro. Attraverso la conversione chimica del carbonio e dell’idrogeno contenuti nei rifiuti si possono ottenere prodotti chimici e carburanti a basso contenuto carbonico, recuperando rifiuti non riciclabili. In breve, i benefici sarebbero 4: decarbonizzazione, riciclo, occupazione e riduzione delle importazioni dall’estero, a tutto vantaggio delle economie locali. Non solo. Per i comuni che ospitano l’impianto, e in misura minore anche quelli che ne usufruiscono, sono previsti una serie di vantaggi fiscali ed economici. Al termine dell’incontro, la società ha lasciato nelle mani degli amministratori una serie di documenti e relazioni, tra cui uno studio curato dall’Università La Sapienza, e si è detta disponibile ad ulteriori momenti di confronto, annunciando anche la possibilità di un tour virtuale in Giappone, dove tutto questo è già realtà.
Nel prendere la parola, il Sindaco Greco ha ringraziato per la presentazione del progetto, oltremodo puntuale e precisa, che ha fornito i primi elementi sui quali avviare ora un’ampia discussione. “Mi fa piacere apprendere che non si tratti di termovalorizzatore, – ha dichiarato – ma mi preme, comunque, evidenziare che la sostanza di quanto da noi affermato nei giorni scorsi non cambia: dev’essere la comunità locale a decidere, dopo essere stata coinvolta e ben informata. E’ una materia estremamente sensibile, e il nostro territorio ha già pagato un prezzo troppo alto in termini di ambiente e di salute, per cui vogliamo valutare secondo scienza e coscienza, dopo approfondite analisi con esperti in materia”. Greco ha sottolineato come la tutela della salute e dell’ambiente vengano al primo posto, e solo dopo precise rassicurazioni in tal senso si potrà parlare di ricadute positive in termini di economia e occupazione, avanzando la possibilità di una esenzione parziale o totale della Tari per i gelesi se la bio raffineria dovesse effettivamente nascere a Gela. “In ogni caso, – ha aggiunto Greco – ci sarà un totale coinvolgimento del consiglio comunale, e a breve annunceremo la data di un monotematico alla presenza di personalità competenti e preparate. E’ logico che la popolazione non voglia neanche sentir parlare di inceneritori, perché immediatamente si pensa a fumi, inquinamento e malattie, ma, come già ampiamente rimarcato, questa amministrazione non vuole intavolare una discussione sulla base di pregiudizi o questioni ideologiche. Pur non accettando scelte calate dall’alto, vogliamo, inoltre, un confronto sereno con la Regione per capire perché la scelta sia caduta proprio su Gela, che già si è spesa tantissimo per aiutare l’intera Sicilia ad uscire dall’emergenza rifiuti, e anche per capire cosa intenda fare, da un punto di vista infrastrutturale, per migliorare i collegamenti viari, ferroviari e marittimi con Gela, nel caso in cui questo impianto dovesse nascere”.
Fonte: Il Quotidiano di Gela del 4 maggio 2022
Gela. Il maxi progetto da oltre 640 milioni di euro, annunciato dal presidente della Regione Nello Musumeci, non è un termovalorizzatore. Sono stati chiari, questa mattina, i manager di MyRechemical e Asja, gruppi del settore che hanno presentato il progetto e che sarà messo in gara. Il governatore siciliano, quindi, avrebbe usato una definizione impropria. Quella che questa mattina è stata descritta in presenza del sindaco Lucio Greco e degli assessori è una “tecnologia pulita”. L’impianto sarà concentrato sul waste to chemical, con la produzione di idrogeno per i biocarburanti. “Non ci saranno combustione dei rifiuti ed emissioni impattanti”, hanno spiegato i manager. In municipio, si è tenuto un primo incontro. C’era l’ingegnere Giacomo Rispoli, ex manager Eni e ora ai vertici del gruppo che intende finalizzare l’investimento. È stata individuata un’area di circa dieci ettari, all’interno dell’area del complesso Eni, in contrada Piana del Signore. “La tecnologia del distretto circolare di NextChem (Gruppo Maire Tecnimont) sviluppata dalla controllata MyRechemical, prevede un sistema per la conversione chimica, mediante un processo di ossidazione parziale, delle molecole di idrogeno e di carbonio contenute negli scarti dei rifiuti, in un gas di sintesi detto syngas, che è un prodotto chimico particolarmente pregiato. Nel processo di conversione chimica il syngas viene purificato prima di essere avviato ai catalizzatori per la produzione di metanolo. I limiti ammessi per i catalizzatori sono molto vincolanti e impongono un controllo in continuo dell’efficienza della purificazione. Dalla ricombinazione del syngas, dopo il processo di purificazione, si ottiene metanolo e idrogeno. Il metanolo trova largo utilizzo sia come solvente che come reagente. La stessa sostanza può essere utilizzata sia come carburante che come vettore energetico o come base per la produzione di nuovi polimeri. Inoltre, il metanolo può essere utilizzato nell’industria del mobile per la produzione di formaldeide, da questo laminati, truciolato e resine. Il metanolo trova crescente uso nella decarbonizzazione dei trasporti marittimi in sostituzione del gasolio bunker, nei porti più attenti alla transizione energetica si stanno predisponendo sistemi di stoccaggio e rifornimento ai natanti di metanolo rinnovabile. Il processo produce anche un residuo vetrificato da frazione inerte (derivante da tracce di sabbia, metalli eventualmente presenti nei materiali trattati) che può essere recuperato e che rappresenta il 16,6 per cento del rifiuto in ingresso. Progetti di ricerca recenti, commissionati da NextChem all’Università di Modena e Reggio Emilia, hanno confermato la natura vetrosa ed inerte del residuo di ossidazione. Le sostanze minerali (come il calcio) e metalliche (come il ferro) presenti nel rifiuto, abbandonano immediatamente il ciclo di conversione e vengono immobilizzate sotto forma di granulato inerte. Questo granulato, sottoposto a varie prove meccaniche e termiche di laboratorio, si è dimostrato idoneo ad essere impiegato come ingrediente per cemento , per abrasivi, per laterizi e per pavimentazioni in gres. La ricerca ha anche evidenziato che il granulato vetrificato, a contatto con ambienti aggressivi acidi o alcalini, conserva il suo stato di inerte e non rilascia sostanze lesive per l’ambiente. La valorizzazione del residuo inerte quale materia prima seconda nel campo edile-civile è un ulteriore aspetto di economia circolare insito nel modello stesso del Distretto Circolare Verde di NextChem. L’impianto Waste to Methanol per Gela è progettato per una capacità produttiva di circa 185.000 ton/anno di metanolo, generate dalla conversione chimica di 400.000 ton/anno di rifiuto (un mix di Plasmix e Fs-Css o rifiuti non pericolosi equivalenti)”, si legge in una nota.
I dati vengono precisati dalle aziende. “L’impianto di Gela produrrà anche circa 3.000 ton/anno di idrogeno circolare, funzionali a una flotta di autobus alimentati a idrogeno e ad una significativa flotta di treni regionali diesel, convertiti ad alimentazione a idrogeno. L’impianto consente di ridurre decisamente le emissioni di anidride carbonica. La CO2 in uscita e’ quasi pura e può essere liquefatta e messa a disposizione di floricoltori e agricoltori per la concimazione carbonica del terreno”, riporta ancora la nota. Sul fronte occupazionale, i manager hanno indicato almeno duecento operatori nel diretto, oltre all’indotto. “Una piccola bioraffineria nella bioraffineria di Eni”, questa è l’intenzione. Greco ha confermato che ci saranno altri incontri di approfondimento e i manager hanno già dato disponibilità a partecipare al consiglio comunale che dovrebbe tenersi proprio sul tema dell’investimento sui rifiuti. “È un primo passo, un segnale positivo – ha detto l’avvocato – come abbiamo spiegato non siamo per un no a priori ma siamo sicuramente contrari a qualsiasi imposizione o a decisioni imposte senza concertazione. La priorità dell’amministrazione è la tutela dell’ambiente e della salute e valuteremo anche le ricadute economiche”. Si è già strutturato un fronte, anche politico, contrario ad impianti per il trattamento dei rifiuti, in una città che rientra tra i siti ad alta incidenza di rischio ambientale per la presenza dell’industria.
Fonte: Hydronews del 2 maggio 2022
Roma – Le hydrogen valley circolari, in cui produrre H2 con la sua tecnologia waste-to-chemical, a cui lavora NextChem (gruppo Maire Tecnimont) potrebbero essere almeno 10-12, “idealmente una per regione”, ma ci sono alcune iniziative in una fase già più avanzata, come quelle formulate in risposta al recente bando della Regione Toscana e quella che prevede la produzione di idrogeno da rifiuti a Gela, in Sicilia, in uno spazio adiacente alla bio raffineria dell’Eni.
A fare il punto sullo stato di avanzamento dei progetti del gruppo è Giacomo Rispoli, Amministratore delegato di MyRechemical, la nuova società costituita da Maire Tecnimont proprio per sviluppare questo tipo di soluzioni, a margine del convegno ‘Idrogeno: iniziative di sviluppo per la mobilità sostenibile e l’industria’, organizzato a Roma da WEC (World Energy Council) Italia e AIDIC.
In Toscana, NextChem è parte dell’ “Alleanza per l’economia circolare” che ha risposto ad un bando della Regione Toscana per la gestione dei rifiuti, proponendo tre ‘distretti circolari’ da realizzare a Empoli, Rosignano Marittimo e Pontedera, basati proprio sulla tecnologia waste-to-chemical del gruppo, “mentre l’Eni ha risposto allo stesso bando con un altro progetto che riguarda la bioraffineria di Livorno e che prevede anch’esso l’utilizzo del nostro sistema, quindi in questo caso sono 4 i progetti che ci vedono coinvolti” ha spiegato Rispoli, aggiungendo poi che l’altro progetto su cui ad oggi la società può svelare dettagli è quello di Gela.
“In Sicilia – ha infatti ricostruito il manager, che viene da una lunga esperienza in Eni – la Regione ha lanciato due bandi relativi a progetti per la gestione di circa 800.000 tonnellate all’anno di rifiuti solidi non riciclabili, dividendo la procedura tra la parte orientale (400.000 tonnellate di rifiuti) e quella occidentale (le altre 400.000 tonnellate) dell’isola. Noi, in partnership con la società Asja di Torino, ci siamo aggiudicati il bando per la Sicilia occidentale”.
Il progetto proposto da NextChem prevede l’utilizzo di queste 400.000 tonnellate di rifiuti per produrre ogni anno circa 3.000 tonnellate di idrogeno low carbon e 190.000 tonnellate di metanolo, “ma le proporzioni, entro certi limiti, sono variabili, e quindi adattabili alla futura evoluzione del mercato”. Quanto all’ubicazione dell’impianto, “l’Eni ci ha messo a disposizione un’area all’interno della sua bioraffineria di Gela, che verrà quindi affiancata da questo innovativo sistema di waste-to-chemical”. Va sottolineato che l’Eni e Maire Tecnimont hanno un consolidato rapporto di collaborazione, confermato ancora di recente con una commessa relativa alla produzione di idrogeno nella bioraffineria di Marghera.
Il modello messo a punto da NextChem consente di dimezzare l’emissione di CO2 rispetto alle tecnologie tradizionali di smaltimento dei rifiuti solidi, e genera CO2 con una concentrazione molto maggiore (vicina al 95%), “caratteristica che permette di mantenerla più facilmente allo stato liquido, agevolando i possibili riutilizzi di questo prodotto di scarto del processo, o anche il suo eventuale stoccaggio definitivo in giacimenti di gas o petrolio ormai esausti, soluzione a cui stiamo lavorando insieme all’Eni”.
Secondo Rispoli, i primi impianti di questo tipo potranno entrare in funzione entro 3-4 anni, producendo idrogeno circolare ad un prezzo finale compreso tra i 3 e i 5 euro al Kg. “Si tratta di un valore già decisamente competitivo, e sopratutto che ha il pregio di mantenersi sostanzialmente stabile nel tempo”. La materia prima del processo non è infatti costituita dal gas, il cui prezzo è sempre più elevato e sopratutto soggetto alle crisi geopolitiche attualmente in atto, ma dai rifiuti, “di cui c’è grande abbondanza. Il loro costo è negativo (chi conferisce i rifiuti paga circa 140-150 euro a tonnellata per il loro smaltimento) e destinato a restare sostanzialmente invariato nel prossimo futuro. “L’unico fattore che può influenzare il prezzo finale del nostro H2 è il costo dell’energia elettrica impiegata, che preleveremo in parte della rete ma che, nei contesti in cui ciò sarà possibile, produrremo anche in loco da fonte rinnovabile, oppure otterremo tramite appositi contratti PPA”.
Fonte Greenreport.it – 27 Aprile 2022
Rispoli: «Una soluzione che consente una riduzione complessiva fino al 90% della CO2 emessa in atmosfera e di produrre prodotti circolari e combustibili di seconda generazione»
È stato presentato ieri al Consiglio comunale di Empoli lo studio di fattibilità per uno dei tre “Distretti circolari” proposti alla Regione, nell’ambito dell’avviso pubblico bandito per provare a colmare con la collaborazione delle imprese il cronico deficit impiantistico che grava sulla gestione rifiuti in Toscana.
Ad intervenire in Palazzo municipale, per illustrare le caratteristiche del progetto, sono stati direttamente i proponenti: Nicola Ciolini e Alberto Irace per Alia, il gestore unico e interamente pubblico dei servizi d’igiene urbana nell’Ato centro; Giacomo Rispoli, in qualità di ad di MyRechemical (NextChem, gruppo Maire Tecnimont); Damien Lebonnois, Innovation manager trattamento e valorizzazione di Suez. Insieme, sono parte integrante dell’Alleanza per l’economia circolare che ha avanzato le proposte progettuali dei Distretti circolari in Toscana.
«Il progetto ha un tasso di innovazione importante e si inserisce in un modello di sviluppo di economia circolare rispondendo anche a un obiettivo di decarbonizzazione», ha dichiarato in apertura la sindaca Brenda Barnini, che ha fortemente voluto quest’appuntamento istituzionale come step fondamentale di un percorso partecipativo, che metta al centro un coinvolgimento della cittadinanza in ogni fase di quella che ad oggi si prospetta come un’opportunità d’investimento sul territorio locale, in particolare nell’area industriale del Terrafino.
Di cosa si tratta? Come ricorda Lebonnois, dall’Alleanza per l’economia circolare sono nate «le tre proposte di distretti circolari, di cui una per la città di Empoli (le altre due riguardano Rosignano Marittimo e Pontedera, ndr), che grazie all’integrazione di tecnologie rinnovabili e della chimica verde saranno in grado di garantire la chiusura del processo “end of waste”», ricavando nuovi prodotti dai nostri rifiuti.
«Il nostro Piano industriale – argomenta Irace, ad Alia – si sviluppa su tre asset principali: digitalizzazione dei processi per l’incremento della raccolta differenziata; nuovi impianti di riciclo meccanico e biologico; distretti circolari per trattare tutti gli scarti non riciclabili meccanicamente, utilizzando le soluzioni tecnologiche più innovative presenti sul mercato».
Ovvero quelle presentate lo scorso autunno da NextChem insieme alla Scuola Superiore Sant’Anna di Pisa, basate sul riciclo chimico.
«Il modello waste-to-chemicals su cui si basa l’impianto – spiega Rispoli –, attraverso il processo di conversione chimica, permetterà infatti per la prima volta di poter recuperare diverse frazioni presenti nei rifiuti, impossibili da riciclare meccanicamente fino a questo momento. Una soluzione che consente una riduzione complessiva fino al 90% della quantità di CO2 emessa in atmosfera e di produrre prodotti circolari e combustibili di seconda generazione “a carbonio riciclato”, quindi a bassa impronta carbonica in linea con la Direttiva europea sulle rinnovabili, contribuendo così all’indipendenza energetica del Paese».
La direttiva Red II emendata secondo la proposta della Commissione europea Fit for 55% prevede infatti al 2030 una riduzione del 13% delle emissioni nel settore trasporti, il che significherebbe un 16%-18% di combustibili rinnovabili in ogni benzina, come i recycled carbon fuel (Rcf, carburanti da riciclo in grado di garantire almeno -70% nelle emissioni di CO2 lungo l’intero ciclo di vita). In prospettiva (2035) il potenziale dei Rcf – come dei vari advanced fuel, biofuel, e-fuel, synthetic fuel – sarà soprattutto nei settori aviazione e trasporto marittimo, ma l’applicazione dei prodotti del riciclo chimico va ben oltre il solo ambito della mobilità.
L’impianto proposto per Empoli può infatti trattare ogni anno circa 200mila ton di rifiuti non riciclabili meccanicamente – si pensi agli scarti della raccolta differenziata (come il plasmix, nel caso della plastica) o al Combustibile solido secondario (Css) ricavato dall’indifferenziata –, e da lì ricavare nuove molecole circolari come l’idrogeno ed il metanolo, vettore energetico che può essere utilizzato sia nella produzione di biocarburanti sia nei cicli produttivi dell’industria chimica.
Un altro elemento d’interesse per il Distretto circolare empolese è sicuramente legato alle potenziali integrazioni con le filiere industriali locali, e in particolare con la vetreria di Zignago: sinergie che secondo i proponenti saranno in grado di generare benefici per entrambe le realtà, dato l’utilizzo di utility comuni, il recupero di cascami termici e l’ottimizzazione del ciclo delle acque, fino all’avvio di un progetto sperimentale per l’alimentazione green dei forni attraverso l’idrogeno prodotto dagli scarti.
«Dai nostri studi di fattibilità – aggiunge nel merito Irace – l’area industriale del Terrafino è risultata tra le migliori in Toscana per ospitare un Distretto circolare, grazie ad una ottima logistica e ad una integrazione con i poli del riciclo meccanico già presenti nell’area industriale. Il riciclo chimico consentirà la chiusura del cerchio dell’economia circolare, in stretta sinergia con le filiere del vetro e della carta che hanno qui su Empoli una storica tradizione. Un investimento previsto di circa 400 milioni di euro, in grado di impegnare circa 600 addetti in fase di costruzione e circa 200 occupati, tra diretti e indiretti, a regime. Si tratta di una soluzione che vogliamo condividere con il territorio e il tessuto sociale locale, raccogliendo istanze e proposte, con l’obiettivo di contribuire finalmente a rendere questo territorio e la Toscana una regione autosufficiente nella gestione e smaltimento dei rifiuti, con benefici misurabili per l’ambiente e le collettività».
Sotto questo profilo la sindaca Barnini ha ribadito che l’Amministrazione vuole che ogni singolo passaggio sia condiviso e reso accessibile alla cittadinanza, e – in attesa di vedere se questo sarà uno dei progetti che la Regione Toscana sceglierà – si attiverà per studiare nuovi strumenti di partecipazione e coinvolgimento dei cittadini, chiedendo massima garanzia in ordine ai temi della salute, del bilancio ambientale che deve essere positivo e delle ricadute sul territorio, sia in termini occupazionali che di una forte riduzione della Tari.
“Estraiamo gas dai rifiuti senza emissioni. Nella Capitale basterebbero due nostri impianti per risolvere il problema” commenta Di Amato
Il tema rifiuti continua a tenere banco sulla Capitale, e non solo. Sulle colonne de Il Tempo, Fabrizio Di Amato, Presidente del gruppo Maire Tecnimont, azienda di ingegneria e contracting per l’industria chimica dagli anni ’30, è intervenuto nel merito, svelando la loro tecnologia per pulire Roma.
Rifiuti
“I rifiuti – afferma Di Amato – sono il petrolio del terzo millennio. E oggi possiamo utilizzarli al 100% per produrre molecole o prodotti riducendo complessivamente le emissioni di CO2. La nostra tecnologia è all’avanguardia nell’estrarre idrogeno e carbonio dai rifiuti plastici e indifferenziati. Valorizzazione rifiuti? È una questione di comunicazione, vanno spiegati i vantaggi di queste nuove tecnologie. I rifiuti che oggi non possono essere riciclati altro non sono che materiale composto da carbonio e idrogeno. Gli stessi mattoni che formano gli idrocarburi. Noi con i nostri processi li recuperiamo e li ricomponiamo senza emissioni. Inceneritori? Noi abbiamo messo a punto una tecnologia avanzata che non incenerisce, ma dagli scarti estrae un gas di sintesi che si può usare per ridurre l’impatto carbonico delle acciaierie, ad esempio, o per realizzare prodotti chimici fondamentali per l’industria e i carburanti verdi. In tutto questo riduciamo complessivamente la CO2 emessa e lo scarto che rimane, circa il 10%, è costituito da materiale inerte da utilizzare nelle coibentazioni dell’edilizia o nell’asfalto stradale”.
“Abbiamo 12 progetti realizzabili in 10 regioni italiane”
“Il Lazio – prosegue – produce alcune centinaia di migliaia di tonnellate di indifferenziata all’anno. Con uno dei nostri impianti potremmo mandare avanti tutta la mobilità pubblica di Roma. Gli impianti dei nostri distretti circolari verdi, che riciclano i rifiuti plastici e trattano quelli indifferenziati per ricavarne carbonio e idrogeno, si possono fare in aree industriali dismesse o in via di abbandono come, ad esempio, le centrali a carbone il cui destino è già segnato. In questo modo innanzitutto si darebbe una risposta concreta alla riqualificazione di siti destinati all’abbandono e nuove opportunità per quei lavoratori da ricollocare in nuove professionalità green. In Italia ci sono già aree industriali mappate, spesso sono raffinerie, la tecnologia c’è e anche i soldi. Il Piano nazionale di ripresa e resilienza stanzia 70 miliardi per iniziative destinate alla transizione green. Sono una quantità di denaro sufficiente per finanziare il cambiamento. I primi bandi sull’economia circolare sono stati pubblicati e noi abbiamo 12 progetti che sarebbero realizzabili in 10 regioni italiane“.
Europa e Roma
“In Europa – rivela Di Amato – la transizione energetica è partita ed è anche un business. Sarà una grande sfida: bisogna evitare gli errori di favorire conflitti tra gli Stati europei nel raggiungere i target. Ognuno ha una vocazione che va rispettata. La Francia punta sul nucleare, la Germania sul gas, noi siamo i più bravi nell’economia circolare e abbiamo un problema, quello della gestione dei rifiuti, che possiamo però trasformare in opportunità. Roma? Siamo pronti. Ci sono i siti industriali dismessi, montagne di rifiuti da trattare e ci sono le discariche. Abbiamo intenzione di proporre la nostra soluzione alla nuova amministrazione. Nella Capitale basterebbero due nostri impianti per risolvere il problema. Contiamo sull’efficacia del decreto semplificazioni che stabilisce una procedura in grado di abbattere i tempi di realizzazione. Oggi solo per un’autorizzazione i tempi medi sono di circa 1.600 giorni. Per costruire il primo sito in Italia di riciclo delle plastiche ci sono voluti circa 8 anni. Troppi per i benefici che sta dando oggi che è pienamente operativo”.
“Premesse per una grande transizione energetica”
“Trattiamo 40mila tonnellate di plastica riciclabile che equivale ai rifiuti plastici di un milione di persone all’anno. Non solo. Il materiale che esce dall’impianto è un polimero rigenerato. I polimeri sono trasformati e riformulati e il grado di purezza di quanto prodotto è elevatissimo. Facciamo impianti grandi come città. L’ultimo in Russia per trattare il gas esportato in Cina. Lavoriamo dove ci sono queste opportunità che in Italia negli ultimi anni non ci sono state, perché è priva di grandi giacimenti di idrocarburi. Ora ci sono le premesse per una grande transizione energetica. E possiamo dire la nostra perché la nostra tecnologia è tra le più avanzate e pulite al mondo” conclude il Presidente del gruppo Maire Tecnimont.
Città e distretti circolari, progetti e idee per la decarbonizzazione (adnkronos.com)
Idee e progetti per la transizione ecologica verso un futuro e emissioni zero. Con un ruolo di primo piano per l’economia circolare. Se n’è parlato a Ecomondo, in occasione del talk ‘Circular cities: economia circolare e decarbonizzazione, la risposta dei distretti circolari’, organizzato dal Gruppo Maire Tecnimont, in collaborazione con l’editore Edizioni Ambiente e con l’Alleanza per l’Economia Circolare, nella prima giornata di Ecomondo alla Fiera di Rimini.
Per NextChem, la società del Gruppo Maire Tecnimont per la transizione energetica, è possibile abbattere le emissioni di CO2 e trasformare gli scarti in risorse grazie al modello dei ‘Distretti circolari’, principalmente finalizzato alla riconversione green di vecchi impianti. Un modello che consente di produrre nuovi materiali dal riciclo di qualità dei rifiuti plastici, prodotti chimici circolari dal riciclo chimico di frazioni di rifiuti e idrogeno verde da energie rinnovabili. “L’idea del distretto circolare nasce prima di tutto dall’esistenza di siti cui dare nuova vocazione industriale. Ci sono siti dismessi, che sono o diventeranno problematici, che hanno una vocazione in termini di maestranze, piccole e medie imprese e di infrastrutture e che in un’economia lineare non avrebbero futuro”, spiega Pierroberto Folgiero, Ceo Maire Tecnimont e NextChem.
Dall’altro lato abbiamo “una carica di alimentazione circolare: ci sono tecnologie mature che possono usare carbonio e idrogeno disponibile nella parte di materia di scarto che non può più prestarsi a riciclo e recupero”. Poi ci sono i prodotti: “Oggi l’Italia importa tantissimi chemicals che si possono produrre in un distretto circolare”. Dunque bisogna “unire i puntini” che significa “unire un territorio che ha una vocazione, pensare ad un prodotto, cercare di capire dove sta la carica, che sono rifiuti secchi o plasmix, trasformarla e, ultimo puntino, la capacità imprenditoriale. Noi siamo pronti a garantire che queste tecnologie funzionano”. Quali gli obiettivi possibili? “La prima grande produzione che si può fare decarbonizzando è quella di carburanti circolari. Ma bisogna considerare che dal gas di sintesi un bravo chimico ricava qualunque prodotto, si possono produrre plastiche, idrogeno, additivi per le vernici, metanolo per formaldeide…”.
E i tempi sono favorevoli per una trasformazione del sistema. Per Fabrizio Di Amato, presidente Gruppo Maire Tecnimont, “l’industria, e un azienda come la nostra, oltre che la possibilità di farlo ha un dovere morale e sociale di cavalcare un momento importante”. “In Italia abbiamo un ministro della Transizione ecologica, capitali a disposizione, pubblici e soprattutto privati. Se noi cataloghiamo la transizione ecologica come qualcosa di sistemico che riguarda tutti e la mettiamo sul binario, più o meno, dell’emergenza sono convinto che tutti convergiamo”, spiega. C’è “l’opportunità per cambiare le cose. Io penso che siamo di fronte ad un momento in cui le cose possono succedere e succederanno, credo che nei prossimi cinque anni ci saranno cambiamenti epocali e grandissime opportunità di lavoro”.
La transizione ecologica ed energetica è questione anche di competenze che abbracciano diverse discipline. “Non è una questione di tecnologia e basta. L’industria si fa con i capitali, gli imprenditori, la regolamentazione e con la tecnologia. Quindi la nuova formazione da fare è orizzontale e unisce competenza sociali, regolamentari, tecniche ed economiche”, osserva Folgiero.
Guardando alle nostre città, secondo Daniele Fortini, presidente RetiAmbiente, “dobbiamo immaginare che la materia usata che è contenuta nei rifiuti urbani può tornare materia. La città resiliente è la città che si occupa con intelligenza del proprio futuro e di quello delle generazioni che verranno, è una città che prova a non sprecare, a consumare in modo intelligente e ad avere stili di vita con un livello di benessere nel modo più coeso e inclusivo e, allo stesso tempo, una visione che preserva e costruisce ma anche progredisce e investe”.
Acciaierie d’Italia, arriva la svolta green | Tarantobuonasera
La decarbonizzazione o la produzione green dell’acciaio o l’acciaio pulito, come è stato definito in questi anni è un processo concreto che sta prendendo corpo all’ex Ilva di Taranto. Il momento della svolta green è finalmente arrivato. Non si tratta di slogan questa volta. Lo dimostra uno studio di fattibilità che sarà avviato a seguito dell’accordo firmato da Acciaierie d’Italia con la NextChem, società del Gruppo Maire Tecnimont (uno dei più grandi e importanti d’Europa) finalizzato alla decarbonizzazione dello stabilimento siderurgico di Taranto. Lo studio, spiega una nota, si concentrerà sull’impiego di gas circolare (Syngas) ottenuto attraverso la tecnologia di riciclo chimico di NextChem, basata sul recupero del carbonio e dell’idrogeno contenuti in scarti plastici e secchi mediante un processo di ossidazione parziale. La tecnologia di NextChem consente di ottenere un gas circolare che può essere utilizzato sia nei processi di raffinazione che nel ciclo produttivo dell’acciaio – in sostituzione di polverino di carbone in altoforno o di gas naturale nella riduzione diretta – per abbattere le emissioni di anidride carbonica.
Lo studio di fattibilità metterà a fuoco i benefici ambientali derivanti dall’impiego del gas circolare in acciaieria, come anche dalla valorizzazione dei gas di coda prodotti nel sito. Pierroberto Folgiero, amministratore delegato del Gruppo Maire Tecnimont e di NextChem, ha manifestato la sua soddisfazione per la firma dell’accordo: «Siamo orgogliosi di collaborare con Acciaierie d’Italia per lo sviluppo di un progetto che può offrire una soluzione concreta per la decarbonizzazione del ciclo produttivo e di lavorazione dell’acciaio. La tecnologia di NextChem, già cantierabile, può dare un grande contributo alla riconversione green dei siti industriali tradizionali». Soddisfatta anche Lucia Morselli, amministratore delegato di Acciaierie d’Italia: «Contribuire alla transizione energetica è precisa responsabilità di ogni impresa. La tecnologia per il gas circolare di NextChem è di interesse per Acciaierie d’Italia perché, una volta verificata, va nella direzione della decarbonizzazione dei nostri impianti».
Rendere green lo stabilimento siderurgico di Taranto rappresenta anche una sfida per le aziende che saranno impegnate. Molto spesso, nel corso degli ultimi anni, si è acceso il dibattito che ha visto protagonisti esponenti politici, sindacati, gruppi e associazioni impegnati nell’ambientalismo e personaggi del mondo della cultura, divisi sul tema dell’ambientalizzazione dell’ex Ilva di Taranto diventata il simbolo dell’inquinamento delle fabbriche che uccidono provocando malattie e morti.
Adesso, invece, le nuove tecnologie consentono di intervenire su impianti costruiti diversi decenni fa per introdurre una produzione che riduca al minimo l’impatto delle emissioni sull’ambiente e sulla salute. Il ministro dello Sviluppo economico Giancarlo Giorgetti, nei giorni scorsi, durante un’audizione alla Commissione Attività produttive della Camera dei Deputati ha sostenuto che l’introduzione di un sistema di produzione “pulito” potrebbe evitare la confisca definitiva degli impianti disposta dalla magistratura. Infatti, in primo grado, la Corte d’Assise di Taranto, nella sentenza, ha disposto la confisca dell’area a caldo. La svolta green, quindi, potrebbe consentire allo Stato, ora socio di Acciaierie d’Italia, di superare l’ostacolo delle vicende giudiziarie e di scrivere una storia diversa da quella degli ultimi anni.
Siglato un accordo con Acciaierie d’Italia per lo studio di fattibilità
Folgiero: «Tecnologia già cantierabile, può dare un grande contributo alla riconversione green dei siti industriali tradizionali»
Dopo anni di tentennamenti, l’ex Ilva di Taranto potrebbe aver trovato un modo per tagliare le emissioni di CO2 legate alla produzione di acciaio, puntando su un’innovazione tecnologica tutta italiana: quella fornita da NextChem (controllata della multinazionale Maire Tecnimont) e basata sul riciclo chimico.
Il principale gruppo siderurgico italiano – ovvero Acciaierie d’Italia, partecipato da ArcelorMittal e Invitalia – ha infatti appena firmato un accordo con NextChem per uno studio di fattibilità sull’impiego nell’acciaieria di Taranto di gas circolare (syngas), ottenuto attraverso la tecnologia di riciclo chimico di NextChem.
Più nel dettaglio, la tecnologia “waste to chemicals” di NextChem prevede un sistema per la conversione chimica, mediante un processo di ossidazione parziale, delle molecole di idrogeno e di carbonio contenute nelle plastiche post consumo e altri materiali solidi secchi – in particolare plasmix e Css – in un gas di sintesi detto syngas, che è un prodotto chimico particolarmente pregiato. Il sistema utilizza come agente di reazione l’ossigeno puro, grazie al quale si genera un syngas libero da azoto e con un più alto potere calorifico. Una volta raffreddato, il syngas viene sottoposto a purificazione da contaminanti e può essere utilizzato come tale, per le sue qualità riducenti, all’interno di processi produttivi come quello siderurgico, in sostituzione del gas di sintesi prodotto dal metano o da derivati del carbone (come il polverino di carbone), abbattendo in questo modo le emissioni climalteranti generate, e con un costo inferiore.
«Contribuire alla transizione energetica è precisa responsabilità di ogni impresa. La tecnologia per il gas circolare di NextChem è di interesse per Acciaierie d’Italia perché, una volta verificata, va nella direzione della decarbonizzazione dei nostri impianti», dichiara l’ad di Acciaierie d’Italia, Lucia Morselli.
Del resto quella siderurgica è una delle principali industrie “hard to abate” con le quali siamo chiamati a confrontarci per far fronte alla crisi climatica, e questo vale in particolar modo per un player delle dimensioni dell’ex Ilva.
L’European steel association (Eurofer) ha già avanzato l’ambizione di ridurre le emissioni di CO2 legate alla produzione di acciaio in Europa del 30% entro il 2030 rispetto ai livelli del 2018 – o del 55% rispetto al 1990 – e di avvicinarsi alla carbon neutrality entro il 2050: la strada per raggiungere l’obiettivo passa in primis dall’innovazione, come mostra l’iniziativa di NextChem che si aggiunge a quella avanzata nei giorni scorsi da Iren per sostituire l’impiego del carbone in acciaieria con il polimero plastico riciclato Bluair.
«Siamo orgogliosi di collaborare con Acciaierie d’Italia per lo sviluppo di un progetto che può offrire una soluzione concreta per la decarbonizzazione del ciclo produttivo e di lavorazione dell’acciaio. La tecnologia di NextChem, già cantierabile – sottolinea l’ad della società, Pierroberto Folgiero – può dare un grande contributo alla riconversione green dei siti industriali tradizionali».
Una tecnologia che la scorsa settimana è stata presentata in dettaglio da NextChem insieme alla Scuola superiore Sant’Anna di Pisa. Proprio in Toscana, peraltro, c’è un altro polo siderurgico in attesa di trovare la sua strada (sostenibile) verso la ripresa: quello di Piombino. Chissà che la collaborazione tra NextChem con l’ex Ilva di Taranto non possa essere d’esempio.
Idrogeno da rifiuti: il ruolo dei porti come futuri ‘distretti green’ secondo NextChem – HydroNews
Installare le tecnologie ‘waste to chemical’ nei principali bacini portuali nazionali per sfruttare i rifiuti prodotti in loco come materia prima da trasformare in combustibili green utili a decarbonizzare le stesse attività marittime e logistiche degli scali.
Un modello a cui guarda con interesse NextChem, società del gruppo Maire Tecnimont focalizzata sulle tecnologie per la transizione energetica, che – non a caso – è coinvolta insieme alla multi-utility Iren nello studio di fattibilità di un progetto per la produzione di idrogeno all’interno del porto di Genova.
“I porti sono dei sistemi complessi, che movimentano ogni giorno persone e merci” ha spiegato Alessandro D’Amati, Business Development Manager di NextChem, nel corso del convegno ‘Green RePort: I numeri della sostenibilità dei porti Italiani’, organizzato nell’ambito del Forum Compraverde Buygreen.
“I porti dell’Autorità di Sistema Portuale del Mar Ligure Occidentale (Genova, Savona e Vado Ligure; ndr) nel 2018 hanno movimentato più di 70 milioni di tonnellate di merce e 4,3 milioni di passeggeri, trasportati da oltre 9.000 navi, con un carbon footprint totale pari a 537.520 tCO2eq, di cui l’80% dovuto a navi in sosta o in manovra, il 19% a operatori portuali e l’1% a veicoli in transito”. Nello stesso anno – ha aggiunto il manager – questi scali “hanno prodotto circa 15.000 metri cubi di rifiuti solidi secchi indifferenziati”. Rifiuti che oggi escono dal porto e vengono conferiti a discarica o a inceneritore, ma che, “con la tecnologia ‘waste to chemical’ di NextChem, potrebbero rimanere nella zona portuale ed essere trasformati in biocarburanti, come idrogeno ed etanolo, che potrebbero sostituire quelli di origine fossile”.
Grazie alla tecnologia messa a punto dalla società del gruppo Maire Tecnimont, i porti potrebbero quindi trasformarsi in “distretti verdi dove attuare processi di economia circolare in linea con gli obbiettivi europei inseriti nel pacchetto ‘Fit for 55’ e con la strategia ambientale di Bruxelles per il 2050”.
di Emanuele Bompan
Idrogeno ricavato da fonti rinnovabili o dalla conversione di rifiuti, riconversione dei vecchi siti produttivi e biocarburanti di nuova generazione: la strategia di NextChem é assai articolata, e contribuisce a quel cambiamento culturale indispensabile perché la decarbonizzazione possa avere successo.
Industrializzare l’innovazione, un tema complesso, soprattutto nei grandi progetti di biochimica e chimica verde, dove ottime idee spesso si arenano per la difficolta di trovare un abilitatore per lo scale-up. Oppure dove la riqualificazione dei brownfield, prevalentemente siti industriali chimici, petrolchimici o siderurgici, da cui partire per avviare o consolidare un percorso di transizione energetica e ridare vita e futuro alle proprie attività, non è semplice. Ma nella grande sfida per la decarbonizzazione dell’industria, un tema centrale, ribadito anche dalla strategia del Green Deal Eu e dal meccanismo Just Transition, è proprio quello di ripensare i distretti della chimica (settore industriale che pesa complessivamente per il 19% delle emissioni di tutta l’industria), agendo su tre fronti chiave: ridurre i consumi di plastica laddove possibile e spingere sul riciclo chimico meccanico dei rifiuti in plastica; decarbonizzare la produzione dell’energia utilizzata nell’industria chimica; “defossilizzare” i feedstock utilizzati per la produzione dei composti chimici di base, senza contare poi la produzione di nuove forme di energia e carburanti low carbon, come waste-to-hydrogen o Hvo e etanolo di seconda generazione. Uno dei grandi protagonisti di questa trasformazione, che guarda alla realizzazione di distretti circolari della chimica, è NextChem, società fondata nel 2018 dal Gruppo Maire Technimont, leader nell’engineering del settore del downstream oil&gas, per occuparsi dello sviluppo di tecnologie e impianti per la transizione energetica. “Il modello di NextChem é pensato proprio per dare una risposta alle principali sfide di questi anni, quella della decarbonizzazione, per mantenere nei limiti la temperatura del pianeta; quella dell’economia circolare, per trasformare gli scarti in nuove risorse e usare queste nuove risorse nei processi produttivi riducendo parallelamente l’estrazione di materie prime e risorse naturali. E infine quella della mobilita sostenibile”, spiega a “Materia Rinnovabile” Pierroberto Folgiero, Ceo di NextChem e del gruppo Maire Tecnimont. Una visione che ha tra gli obiettivi la creazione
di un ideale “distretto circolare” dove sviluppare le tecnologie del presente e del futuro per una chimica circolare e per realizzare carburanti e fonti di energia innovative, business case che siano sempre più attraenti per i capitali verdi, scalabili e industrializzabili. Un modello funzionale alla riconversione dei siti industriali cosiddetti brownfield, prevalentemente siti industriali chimici, petrolchimici o siderurgici, che devono avviare o consolidare il proprio percorso di transizione energetica e ridare vita e futuro alle proprie attività, un futuro sostenibile.
L’idrogeno della transizione è circolare
Quella dell’idrogeno circolare è una proposta targata NextChem che trova ampio spazio nel dibattito incorso a livello globale sul ruolo dell’idrogeno low carbon o fossilfree nell’economia del futuro. “L’idrogeno verde, prodotto a partire da fonti di energia rinnovabile è certamente la strada del futuro, ma i costi sono ancora molto alti (circa quattro volte quelli dell’idrogeno convenzionale da steam reforming) e gli aspetti legati alla continuità energetica ancora non rendono questa tecnologia applicabile nell’immediato per i processi industriali, che necessitano di una costanza nell’approvvigionamento e di una sostenibilità economica, in assenza di incentivi”, spiega Folgiero.
Già oggi possiamo invece produrre idrogeno utilizzando rifiuti,a un costo competitivo con i fossili e, in questo modo, anche incentivarne il riciclo. Questo processo rappresenta un agevolatore verso una produzione completamente green entro i prossimi 20-30 anni.
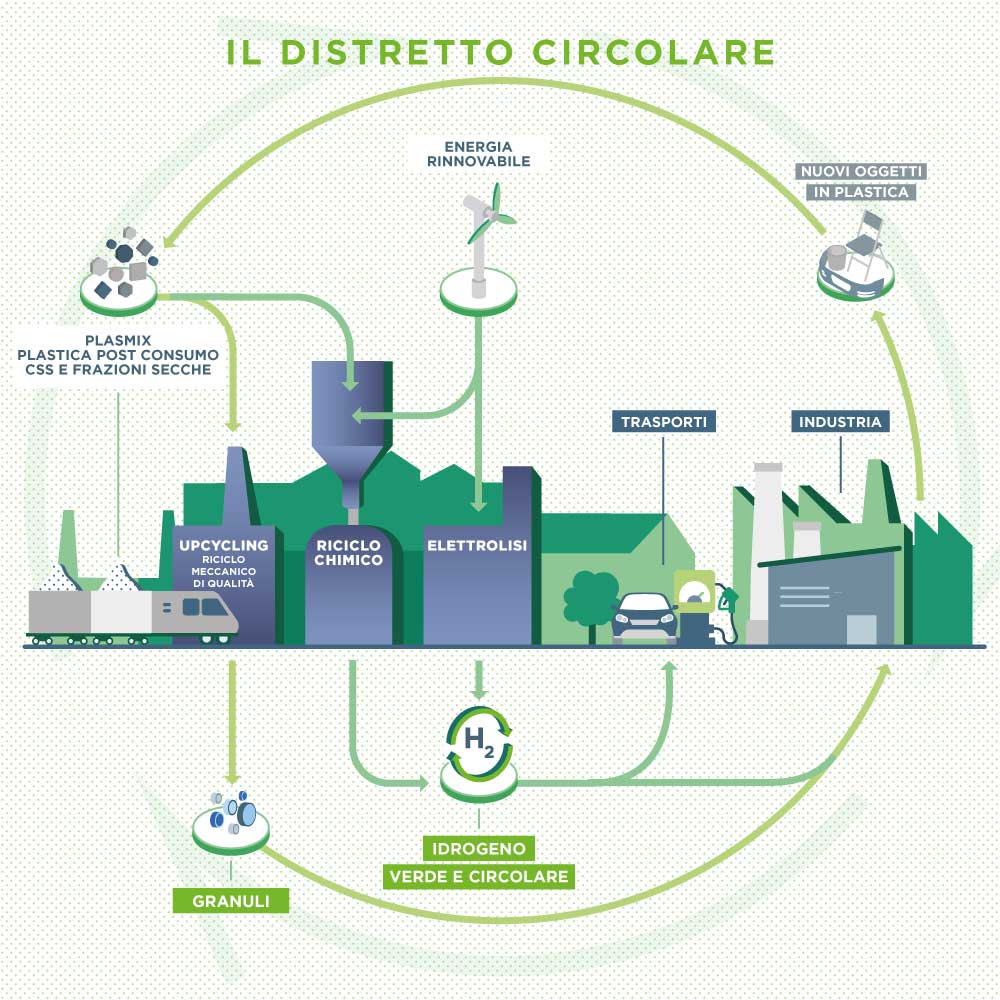
La piattaforma tecnologica NextChem per la produzione di idrogeno e altri chemicals “circolari” si basa su un processo di ossidazione parziale ad alta temperatura, che produce un gas di sintesi che poi viene trasformato in idrogeno o altri prodotti chimici o carburanti, come il metanolo e l’etanolo.
Una tecnologia che potrebbe integrare anche l’elettrolisi, per migliorare ulteriormente la carbon footprint. La tecnologia per produrre idrogeno a partire dalla conversione chimica di rifiuti quali plasmix e Css (combustibile solido secondario, derivato dalla lavorazione dei rifiuti urbani non pericolosi e speciali non pericolasi) permette una riduzione dell’impatto carbonico con un abbattimento fino all’80% della CO, se comparata con l’idrogeno grigio, ovvero tradizionale, da steam reforming.
Oltre al vettore energetico, dal gas di sintesi si possono produrre anche metanolo oppure ammoniaca (NH3). La NH3, stoccabile liquida e a bassa pressione, contiene una quantità di idrogeno (H) importante, seconda solo al metano (NH,), che può essere usata come succedaneo nelle fuell cell oppure essere impiegata come carburante meno carbon-intensive nel settore navale. Con Eni si stanno sviluppando i primi due progetti italiani di impianti per la produzione di idrogeno e di metanolo da conversione chimica di plastiche e materiale secco da rifiuto. Questi impianti nasceranno rispettivamente presso le raffinerie di Porto Marghera e di Livorno, mentre recentemente è stato annunciato uno studio preliminare alla possibile conversione della raffineria di Taranto per produrre gas di sintesi per idrogeno per alimentare i processi di idrodesolforazione dei carburanti, e un gas ricco di ossido di carbonio che potrebbe essere impiegato nella vicina acciaieria, sia nei processi in altoforno sia nelle nuove tecnologie Dri (Direct Reduced Iron), contribuendo alla decarbonizzazione dell’industria siderurgica. Un altro importante processo “circular” è il Waste to Ethanol, sviluppato con LanzaTech, leader delle carbon recycling technology. Il processo base del riciclo chimico si integra con un processo che dal gas circolare (come quello che verrà prodotto a Marghera e Livorno), tramite la tecnologia biologica LanzaTech di syngas fermentatíon potrà generare etanolo sfruttando batteri bioingegnerizzati.
L’etanolo, che in Italia viene totalmente importato, è anche un intermedio importante per una serie di componenti chimici, quali l’etil-acetato — un solvente pregiato per le vernici auto di cui l’Europa è forte importatore — e l’alcol, utilizzato come disinfettante. Essendo derivanti dal riciclo, questi prodotti chimici promuovono modelli circolari di consumo.
Una nuova generazione dl carburanti
Un altro pezzo importante del modello Nextchem sono i carburanti di seconda generazione, attraverso l’uso di biomasse non food, che costruiscono il segmento delle tecnologie Green dell’azienda. Uno degli accordi più interessanti siglati da NextChem è quello con l’azienda brasiliana Granaio e dedicato alle biotecnologie industriali: lo sviluppo e la commercializzazione della licenza di GranBio 2G Ethanol per la produzione di etanolo a base cellulosica. 2G sta per seconda generazione, poiché usa le biomasse non destinate al settore alimentare in biocarburanti rinnovabili e a bassa intensità di carbonio.”Noi offriremo le competenze nell’area Epc (Engineering, Procurement e Construction) e la presenza globale del gruppo per offrire servizi integrati, dagli studi di fattibilità all’integrazione di filiera e alla costruzione di impianti produttivi in tutto il mondo. In questo modo contribuiremo al processo di decarbonizzazione del settore dei carburanti in un modo efficiente, redditizio e neutrale dal punto di vista carbonico”, spiega Folgiero. Al momento a Sao Miguel dos Campos, in Alagoas, Brasile, è attivo il primo impianto, con una capacità produttiva di 30 milioni di litri/anno; inoltre, il 100% del biocarburante può essere potenzialmente esportato verso i mercati americano ed europeo.
Un impianto multi-materia poiché si possono usare ogni tipo di rifiuti agricoli e biomasse a base ligneo-cellulosica, come la paglia, il miscanto, le bucce del mais e scarti lignei come quelli dell’eucalipto e del pino.
Nel segmento del diesel rinnovabile (Hydrotreated Vegetable Oil, detto Hvo) è ben avviata la collaborazione con la società statunitense Saola Energy per la diffusione di una tecnologia chiavi in mano, altamente modularizzata, che consiste in una fase di idro-trattamento seguita da una di isomerizzazione per produrre Diesel rinnovabile di alta qualità, a partire da oli e grassi residui. Si tratta di un modello di bioraffineria di piccola taglia (da 30.000 a 90.000 tonnellate/anno), adattabile anche per bioraffinerie integrate. Integralmente sostituibile al Diesel tradizionale, l’Hvo può costituire una tecnologia di transizione di medio periodo, facilmente impiegabile in tanti paesi in via di sviluppo e in mercati dove la domanda di carburanti per uso di autotrasporto con mezzi pesanti è primaria. “Il vantaggio è che questi impianti sono realizzabili direttamente dove si produce la biomassa di scarto, riducendo i costi di logistica e i tempi di approvvigionamento e massimizzando l’uso delle risorse locali”, continua Folgiero.
Idrogeno verde e superblu
Il 75% dell’idrogeno viene prodotto tramite steam reforming del gas naturale. Si definisce “idrogeno grigio” ed è responsabile (insieme al reforming del carbone) di circa il 3% delle emissioni globali di CO2.Questo perché il carbonio contenuto nella fonte fossile viene direttamente scaricato all’atmosfera durante il ciclo produttivo. Mentre numerose compagnie come Eni stanno promuovendo attivamente progetti con cattura e uso della CO2 (idrogeno blu), cresce lo sviluppo di progetti per l’idrogeno verde, che ha costi superiori ma impatti ambientali decisamente ridotti. In queste tecnologie stanno investendo paesi come la Germania che ha allocato 9 miliardi di euro nei piani di ripresa per generare il primo elemento della tavola periodica e la Francia, con 2 miliardi di euro che saranno finanziati tramite la Recovery and Resilience Facility. Il Gruppo Maire Tecnimont vuole posizionarsi nel ruolo di “front runner” per l’applicazione della tecnologia dell’elettrolisi per la produzione di idrogeno green e nel segmento super-blue, che impiega energie rinnovabili come mezzo per il riscaldamento termico dei forni di reforming. Al momento, l’idrogeno verde rappresenta solo il 2% della produzione a causa di costi molto alti (tra i 3,5 e i 5 euro/chilo, contro 1,50 euro/chilo del grey hydrogen). Tuttavia, secondo La IEA il crescente prezzo della CO2e la riduzione dei costi delle rinnovabili, che per il solare fotovoltaico dovrebbe assestarsi su 1,3 centesimi di euro/KWh, renderanno nel breve termine questa tecnologia assolutamente competitiva. “In questa fase di transizione, prima che il Green hydrogen raggiunga la maturità, il Blue hydrogen, il Super Blue hydrogen e il Circular hydrogen avranno un ruolo fondamentale in ottica lowcarbon”, spiega Pierroberto Folgiero.
“Lo sviluppo del settore dei biocarburanti, inevitabile nel percorso transitorio verso l’elettrico e comunque fondamentale per alcuni segmenti del settore dei trasporti, pone un tema gigante di upstream”,commenta Folgiero. “Occorre uno sforzo per trovare nuove soluzioni per incrementare i feedstock non-food di origine vegetale, che hanno disponibilità limitata e problemi di logistica e di conservazione ancora da affrontare. Lo sviluppo di tecnologie che usano i rifiuti come feedstock è una strada indispensabile, sia in termini transitori sia di prospettiva, per colmare il gap delle fonti advanced, che attualmente sono limitatissime. Per percorrere questa strada va fatto uno sforzo culturale, oltre che tecnologico: bisogna unire la visione dell’economia circolare alla visione della bio economia, studiando le sinergie e promuovendo le simbiosi tra settori. Ma, soprattutto, bisogna porsi nell’ottica di considerare i rifiuti come materia prima pregevole, non come scarti da eliminare e come problema sanitaria da risolvere.